I. Integrated GSSMaker / For GPS/JIPS
1. The Flow of Process from Risk Assessment to the GSS Creation
The diagram below outlines the flow of process, from risk assessment to creation of a GSS, using various functions of BIGDr.
1.1 The basic flow of process under the JIPS from risk assessment to GSS creation
Step 1: Select substances for risk assessment
|
|
![]() |
|
Step 2: Gather information[Types of information to gather]
[Things to consider in the process of gathering information]
|
|
![]() |
|
Step 3: Allocate substances into risk assessment priorities
|
|
Perform risk assessment of each substance in the order of Priorities allocated in Step 3.![]() |
|
Step 4: Develop a Base Set of Information required for risk assessments (Identify and fill the information gaps)
|
|
![]() |
|
Step 5: Characterize Hazard
|
Step 6: Assess Exposure
|
![]() |
|
Step 7: Conduct Risk Characterization
|
|
![]() |
![]() Return to [Step 6: Assess Exposure] Repeat the steps until there is no more concern for risks (RCR < 1) by refining the exposure scenarios. |
Step 8: Document Risk Assessment Process and Publish Relevant OutcomesCreate a GPS/JIPS safety summary (GPS Safety Summary: GSS) in accordance with the generic template and register it on the ICCA website. |
|
![]() Repeat the processes for the next substance [Step 4: Develop a Base Set of information required for risk assessment] |
1.2 The Flow of Process from Risk Assessment to a GSS Creation using BIGDr
1.2.1 For substances whose information are available in the GSSMaker
Step 1: Select substance for risk assessment
|
|
![]() |
|
Step 2: Gather information[Types of information to gather]
|
|
![]() |
|
Step 3: Allocate Substances into Risk Assessment Priorities → Not necessary(Priority allocation of substances is not necessary when selecting substances from the chemical DB of GSSMaker, which contains only about 20 substances.) |
|
![]() |
|
Step 4: Develop a Base Set of Information required for risk assessment → Not necessary(The Base Set of information is already stored in the chemical DB of GSSMaker.) |
|
![]() |
|
Step 5: Characterize Hazard → Not necessary(Hazard characterization has already been conducted for the substances in the chemical DB of GSSMaker) |
Step 6: Assess Exposure
|
![]() |
|
Step 7: Conduct Risk Characterization
|
|
![]() |
![]() Return to [Step 7: Conduct Risk Characterization] Repeat the steps until there is no more concern for risks (RCR < 1) by refining the exposure scenarios. |
Step 8: Document Risk Assessment Process and Publish Relevant Outcomes
|
|
![]() Repeat the processes for the next substance [Step 4: Develop a Base Set of information required for risk assessment] |
1.2.2 For substances whose information are not available in GSSMaker
(Includes when using the substance information that a user has gathered, instead of the information stored in GSSMaker.)
Step 1: Select substances for risk assessment
|
|
![]() |
|
Step 2: Gather information[Types of information to gather]
|
|
![]() |
|
Step 3: Allocate Substances into Risk Assessment Priorities
|
|
![]() |
|
Step 4: Develop a Base Set of information required for risk assessment
|
|
![]() |
|
Step 5: Hazard Characterization
|
Step 6: Exposure Assessment
|
![]() |
|
Step 7: Conduct Risk Characterization
|
|
![]() |
![]() Return to [Step 7: Conduct Risk Characterization] Repeat the steps until there is no more concern for risks (RCR < 1) by refining the exposure scenarios. |
Step 8: Document Risk Assessment Process and Publish Relevant Outcomes
|
|
![]() Repeat the processes for the next substance [Step 4: Develop a Base Set of information required for risk assessment] |
2. Points to Check when RCR > 1 in TRA Calculation
GSSMaker is designed so that a GPS Safety Summary cannot be created when any TRA results in an RCR > 1. Therefore, points to check in case of an RCR > 1 are summarized to serve as a reference in reducing the RCRs below 1. In addition, three sets of checklists are prepared to correspond to the three types of mode (Tier I - Easy mode, Tier I - Normal mode, Tier II mode) available in GSSMaker.
Points shared across all the modes and exposure targets: |
---|
Are the hazard reference values appropriate?
|
(1) RCR > 1 in Tier I - Easy mode | ||||||||||||||||
---|---|---|---|---|---|---|---|---|---|---|---|---|---|---|---|---|
Check the following points before advancing to the Tier I - Normal mode.
|
(2) RCR > 1 in Tier I - Normal mode | ||||||||||||||||||||
---|---|---|---|---|---|---|---|---|---|---|---|---|---|---|---|---|---|---|---|---|
Check the following points before advancing to Tier II mode. Italicized points are the same as in (1). Please skip ahead if these points have already been checked.
|
(3) RCR > 1 in Tier II mode | ||||||||||||||||||||||
---|---|---|---|---|---|---|---|---|---|---|---|---|---|---|---|---|---|---|---|---|---|---|
Check the following points and double check the points described in (1) and (2) again.Please consult an expert if an RCR remains >1 even after confirming all the points below. Italicized points are same as in (1) and (2). Please skip ahead if these points have already been checked.
|
Notes |
---|
|
3. How to derive the hazard assessment values from key study
- The Ministry of the Environment: Preliminary Assessment of Environmental Risk
- NITE/CERI etc.: Initial Risk Assessment Reports
- OECD: SIDS
Please refer to the following document for how to derive the hazard assessment values from key studies.
https://www.jcia-bigdr.jp/jcia-bigdr/doc/document/key_study.pdf[Japanese]
II. How to select PROC (Process Category)
1. How to select PROC (Process Category)
PROC selection flowchart/checklist and the latest descriptor list are summarized in order to aid the appropriate selection of PROCs (process categories) when building worker exposure scenarios with the GSSMaker Worker Tool. The PROCs consist of 28 categories of typical activities and processes at workplaces for the objective of conducting worker exposure assessment under EU REACH. For example, PROC7 is defined as tasks involving industrial spraying, whereas PROC10 is defined as tasks involving roller application or brushing. The amounts of worker exposure can be estimated with the GSSMaker Worker Tool by selecting the appropriate PROCs and other conditions.EU ECHA: Descriptor list for Process categories (see page 50)
flow chart / check list
The 3-step process to help select PROC is shown below: “flow chart of sampling/transfers”, “checklist of high exposure process” and “flow chart of general process”.- First step: flow chart of sampling/transfers
- Second step: High exposure process
- Third step: General process
- Covers mixing or blending of solid or liquid materials in the context of manufacturing or formulating sectors, as well as upon end use
- Charging/discharging of the blending vessel and sampling are considered separate activities and are not included in this PROC.
- Processing of large surfaces at elevated temperature
- e.g., calendering of textile, rubber, or paper
- Air dispersive techniques, i.e., dispersion into air (=atomization) by, e.g., pressurized air, hydraulic pressure or centrifugation, applicable for liquids and powders. Spraying for surface coating, adhesives, polishes/cleaners, air care products, blasting.
- The reference to ‘industrial’ means that workers involved have received specific task training, follow operating procedures and act under supervision. Where engineering controls are in place, they are also operated by trained personnel and regularly maintained according to procedures. It is not meant that the activity can only take place at industrial sites.
- This includes application of paints, coatings, removers, adhesives or cleaning agents to surfaces with potential exposure arising from splashes.
- This PROC can also be assigned to tasks such as cleaning of surfaces using long-handle tools.
- Air dispersive techniques, i.e., dispersion into air (=atomization) by, e.g., pressurized air, hydraulic pressure or centrifugation, applicable for liquids and powders. Includes spraying of substances/mixtures for surface coating, adhesives, polishes/cleaners, air care products, blasting
- The reference to ‘non-industrial’ is to differentiate where conditions mentioned in PROC7 cannot be met. It is not meant that the activity can only take place at non-industrial sites
- Use of substances to facilitate the process of production of foams by forming gas bubbles in a liquid mixture.
- It can be either a continuous or a batch process.
- Treatment of articles by dipping, pouring, immersing, soaking, washing out or washing in substances.
- Includes handling of treated objects (e.g., from/to treatment basin, after drying, plating).
- The service life of the article after the treatment needs to be reported separately.
- This covers processing of mixtures and/or substances into a defined shape for further use
- Covers metal working processes where the lubricants are exposed to high temperature and friction, e.g., metal rolling/forming processes, drilling and grinding, etc.
- Transfers for refilling or discharging from/to reservoirs are not covered.
- Use of lubricant or greasing agents in high kinetic energy conditions, including manual application.
- It does not refer to any filling operation.
- Addresses tasks where exposure of hands and forearms can be expected; no dedicated tools or specific exposure controls other than PPE can be put in place.
- Examples are manual mixing of cement and plasters in construction works or mixing of hair dyes and bleaches.
First step: flow chart of sampling/transfers
[flow chart of sampling]
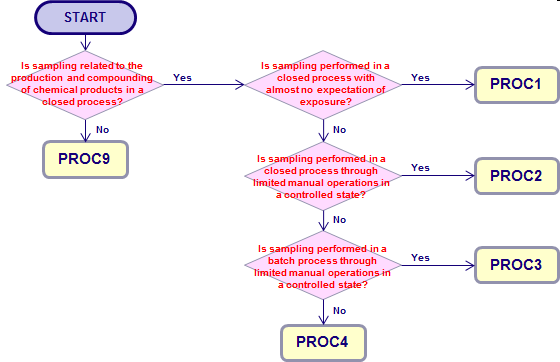
[flow chart of transfers]
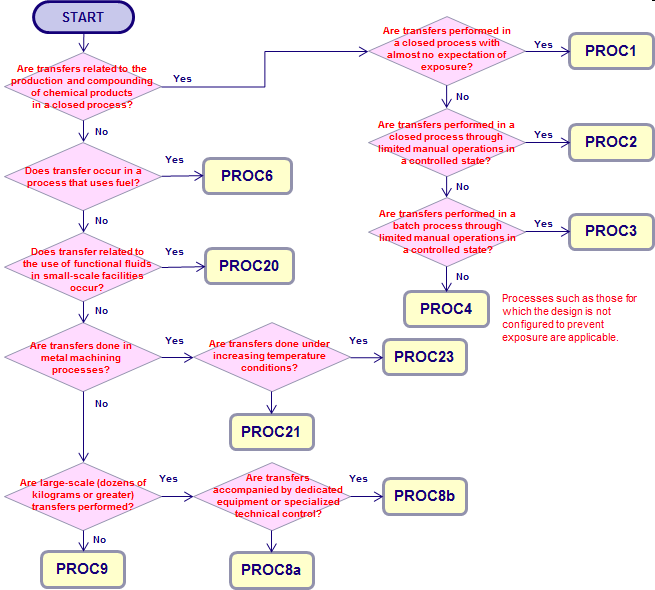
Second step: High exposure process
[check list of High exposure process]PROC No. | Question | Check |
---|---|---|
PROC5 |
Are solid or liquid materials mixed and stirred in the batch process?
[Description of ECHA guidance] |
|
PROC6 |
Are calendering operations performed?
[Description of ECHA guidance] |
|
PROC7 |
Are industrial spray operations performed?
For example, operations such as surface coating, adhesion, surface treatment/cleaners, air care, and blast spraying are applicable. Criteria for determining if a spray operation is for “industrial use” determines not only if the operation is implemented at an industrial facility but also if the operation is performed under appropriate technical control. For details, see the following reference. If the operation is not applicable to industrial use, then confirm PROC11. [Description of ECHA guidance] |
|
PROC10 |
Are roller or brushing operations performed?
The point is to determine if potential exists for exposure due to splashing. [Description of ECHA guidance] |
|
PROC11 |
Are non-industrial spray operations performed?
Criteria for determining if a spray operation is for “non-industrial use” are not to determine whether the operation is performed at a facility other than an industrial facility but to determine whether the operation is not performed under appropriate technical control. [Description of ECHA guidance] |
|
PROC12 |
Are operations that use a foaming agent in the production of foaming products performed?
Both continuous and batch processes are applicable. [Description of ECHA guidance] |
|
PROC13 |
Are molded product treatments through dipping or pouring performed?
Operations such as dipping, rinsing, and washing (with a detergent) are applicable. [Description of ECHA guidance] |
|
PROC14 |
Are the operations of tablet formation, compression, extrusion, pellet formation, and granulation performed?
[Description of ECHA guidance] |
|
PROC17 |
Is lubricating oil injected under high-energy conditions in metal operation processes?
Operations such as metal rolling and molding processes as well as metal excavation and grinding processes are applicable. [Description of ECHA guidance] |
|
PROC18 |
Are operations that use ordinary grease agents or lubrication under high-kinetic-energy conditions performed?
This description includes not only machine operations but also processes with manual operations. [Description of ECHA guidance] |
|
PROC19 |
Are any types of manual operations that include contact with the hands performed?
This description includes, for example, manual cement-mixing processes, mortar production processes, and processes that involve mixing hair dye and bleach. [Description of ECHA guidance] |
Third step: General process
[flow chart of general process]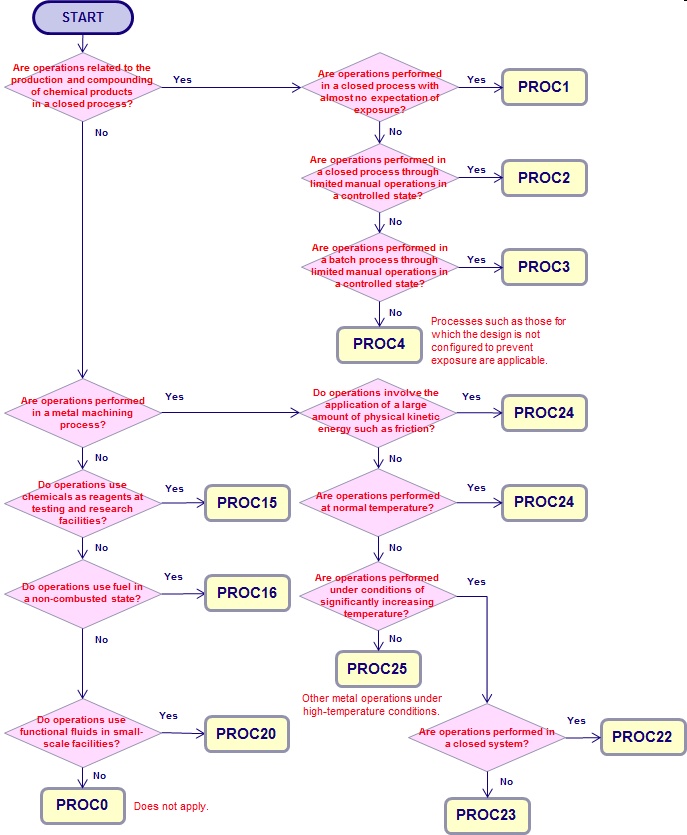